Dr Steve Morrell is a minerals processing engineer with over 40 years of specialist experience in the resources industry. Steve has been involved in the circuit design of the majority of major comminution circuits internationally, through which he has established himself as a world leading expert in comminution design and optimisation.
Steve graduated with a Bachelor's Degree (Honours) in Engineering Science majoring in Metallurgy from Imperial College in London and spent the next 7 years gaining practical, real-world experience working on mines throughout Africa. In the late 1980's, Steve moved to Australia and completed Masters and Doctorate theses in grinding mill simulation and power draw modelling at the Julius Kruttschnitt Mineral Research Centre (JKMRC). Up untill 2000, when he left the JKMRC to start his own consulatnacy (SMCC Pty Ltd), Steve also led world-leading research projects such as the AMIRA P9, High Pressure Grinding Rolls, Fine Grinding and Mine-to-Mill programs and contributed significantly to many industry breakthroughs that helped improve our understanding of modern comminution processes and technologies.
In 2003, based on his extensive practical and research-based experience, Steve founded SMC Testing Pty Ltd to license the innovative SMC Test® – a laboratory comminution test which provides a range of information on the breakage characteristics of rock samples for use in the mining/minerals processing industry. To date, over 50,000 tests have been conducted globally, supporting that the SMC Test® is one of the most useful, versatile and cost-effective rock breakage test procedures available.
In 2016, the Global Mining Standards and Guidelines Group (GMSG) recognised the SMC Test® through the adoption of its guideline “Morrell method for determining comminution circuit specific energy and assessing energy utilization efficiency of existing circuits”
In 2011 Steve was recognised for his significant contribution to the field of comminution when he was awarded the prestigious Art MacPherson Award by the Canadian Mineral Processors Society of CIM. In 2018 he was inducted into International Mining Technology’s hall of Fame and in 2020 it was announced by the AusIMM that he had been given its Professional Excellence award.
Publications List
1. MORRELL, S., 2011. The Appropriateness of the Transfer Size in AG and SAG Mill Circuit Design, Proc International Autogenous and Semi Autogenous Grinding Technology,Vancouver,.
2. MORRELL, S., 2011. Mapping Orebody Hardness Variability for AG/SAG/Crushing and HPGR Circuits, Proc International Autogenous and Semi Autogenous Grinding Technology,Vancouver,.
3. MORRELL, S., 2010, Predicting the specific energy required for size reduction of relatively coarse feeds in conventional crushers and high pressure grinding rolls, minerals engineering Volume 23, Issue 2, January, Pages 151-153
4. MORRELL, S., 2009.,Predicting the overall specific energy requirement of crushing, high pressure grinding roll and tumbling mill circuits, Minerals Engineering, Vol 22, No 6
5. MORRELL, S., 2008, Predicting the Overall Specific Energy Requirements of AG/SAG, Ball Mill and HPGR Circuits on the Basis of Small-Scale Laboratory Ore Characterisation Tests, Proceedings Procemin Conference, Santiago, Chile
6. MORRELL, S., 2008, A method for predicting the specific energy requirement of comminution circuits and assessing their energy utilisation efficiency, Minerals Engineering, Vol. 21, No. 3.
7. MORRELL, S., 2007. The Effect of Aspect Ratio on the Grinding Efficiency of Open and Closed Circuit AG/SAG Mills. Proc. Ninth Mill Operators Conf., AusIMM, pp121–124
8. MORRELL, S., 2006., AG/SAG Mill Circuit Grinding Energy Requirement - How to Predict it from Small Diameter Drill Core Samples Using the SMC Test, Advances in Comminution (Ed. Komar Kawatra), Society for Mining, Metallurgy and Exploration, pp 115-130
9. MORRELL, S., 2006. Rock Characterisation for High Pressure Grinding Rolls Circuit Design, Proc International Autogenous and Semi Autogenous Grinding Technology,Vancouver, vol IV pp 267-278.
10. MORRELL, S.,2004, A new autogenous and semi-autogenous mill model for scale-up, design, and optimisation. Minerals Engineering 17 (2004) 437-445
11. MORRELL, S., 2004. Predicting the Specific Energy of Autogenous and Semi-autogenous Mills from Small Diameter Drill Core Samples. Minerals Engineering, Vol 17/3 pp 447-451
12. MORRELL, S., 2004. An Alternative Energy-Size Relationship To That Proposed By Bond For The Design and Optimisation Of Grinding Circuits. International Journal of Mineral Processing, 74, 133-141.
13. MORRELL, S. (2003). The influence of feed size on autogenous and semi- autogenous grinding and the role of blasting in its manipulation. Proceedings of the XXII International Mineral Processing Congress, Cape Town, South Africa, pp 526-533, SAIMM.
14. MORRELL, S. (2003). Grinding mills: how to accurately predict their power draw. Proceedings XXII International Mineral Processing Congress, Cape Town, South Africa, 29 September - 3 October 2003, pp 50-59, SAIMM.
15. MORRELL, S., 2001. Large diameter sag mills need large diameter ball mills - What are the issues? SAG 2001, Vancouver, B.C. Canada, pp 179-193,
16. MORRELL, S. (2000). Examining recent developments in the design and optimisation of crushing and grinding circuits to reduce costs and improve throughput and quality. Crushing and Grinding Technologies for Mineral Extraction, Perth, pp IIR Pty Ltd.
17. MORRELL, S. (2000). Optimising the performance of your comminution circuit using computer simulation. 2nd Annual Crushing and Grinding in Mining Conference, Jo'Burg, pp IIR Pty Ltd.
18. MORRELL, S. (1996). Design of comminution circuits using laboratory scale tests and simulation techniques. Minerals and Materials '96 Conference, South Africa, pp 219-226,
19. MORRELL, S. (1996). Power draw of wet tumbling mills and its realtionship to charge dynamics Part 2 an empirical approach to modelling of mill power draw. Tran Inst. Min. Met Vol 105: C54-62.
20. MORRELL, S. (1996). Power draw of wet tumbling mills and its relationship to charge dynamics. Part 1 a continuum approach to mathematical modelling of mill power draw. Tran Inst. Min. Met Vol 105: C43-53.
21. MORRELL, S. (1994). Power draw of grinding mills its measurement and prediction. 5th Mill Operators Conf, Roxby Downs, pp 109-114, AusIMM.
22. MORRELL, S. (1992). Prediction of grinding mill power. IMM Transactions Section C Vol 101 (C1-60): 25-32
23. MORRELL, S. (1992). The simulation of autogenous impact breaking. Comminution - Theory and Practice. S.K.Kawatra pp 369-380
24. MORRELL, S., FINCH, W. M., KOJOVIC, T. and DELBONI, H. (1996). Modelling and simulation of large diameter autogenous and semi autogenous mills. Inernational Journal of Mineral Procesing Vol 44-45: 289-300.
25. MORRELL, S. and STEPHENSON, I. (1996). Slurry discharge capacity of autogenous and semi autogenous mills and the effect of grate design. Inernational Journal of Mineral Procesing Vol 46: 53-72.
26. MORRELL, S. and MORRISON, R. (1989). Ore charge, ball load and material flow effects on an energy based SAG mill model. SAG Milling Conf 89, Murdoch University WA, pp
27. MORRELL, S., JOHNSON, G. and REVY, T. (1991). A comparison through observation and simulation of the power utilisation and performance of two dissimilar comminution plants. Fourth Mill Operators Conf, Burnie, Tasmania, pp 157-160,
28. MORRELL, S., NAPIER-MUNN, T. J. and ANDERSEN, J. S. (1992). The prediction of power draw in comminution machines. Comminution theory and practice. S. K. Kawatra pp 233-247.
29. MORRELL, S., STERNS, U. J. and WELLER, K. R. (1993). The application of population balance models to very fine grinding in tower mills. XVIII Int MIn Proc Cong, Sydney, pp 61-66,
30. MORRELL, S., DUNNE, R. C. and FINCH, W. (1993). The liberation of a grinding circuit treating gold bearing ore. XVIII Int Min Proc Cong, Sydney, pp 197-202,
31. MORRELL, S. and KOJOVIC, T. (1996). The influence of slurry transport on the power draw of autogenous and semiautogenous mills. Proc SAG '96, Vancouver, pp 373-389,
32. MORRELL, S. and MORRISON, R. (1996). AG and SAG mill circuit selection and design by simulation. Proc SAG '96, Vancouver, pp 769-790,
33. MORRELL, S. and MORRISON, R. (1997). Making the most efficient use of comminution equipment for effective mineral processing. IIR Conf, Perth, pp
34. MORRELL, S., LIM, W., SHI, F. and TONDO, L. A. (1997). Modelling of the HPGR crusher. SME Annual Meeting, Colorado, pp 117-126,
35. MORRELL, S. and MAN, Y. T. (1997). Using modelling and simulation for the design of full scale ball mill circuits. Mineals Engineering Vol 10 (12): 1311-1327.
36. MORRELL, S., SHI, F. and TONDO, L. A. (1997). Modelling and scale up of high pressure grinding rolls. Proc XX IMPC, Aachen, pp 129-140,
37. MORRELL, S. and LATCHIREDDI, S. (2000). The operation and interaction of grates and pulp lifters in autogenous and semi-autogenous mills. Seventh Mill Operator's Conference, Kalgoorlie, WA., pp 13-19, AusIMM.
38. MORRELL, S. and MUNRO, P. D. (2000). Increased profits through the mine and mill integration. After 2000-the future of mining, Sydney, NSW, pp 194-198, AusIMM.
39. MORRELL, S. and LATCHIREDDI, S. (2001). The operation and interaction of grates and pulp lifters in autogenous and semi-autogenous mills. The AusIMM Proceedings. Vol 306 (1): 59-64.
40. MORRELL, S. and VALERY, W. (2001). Influence of feed size on AG/SAG mill performance. SAG 2001, Vancouver, pp 203-214, Dept of Mining and Mineral Process Engineering, Univ of British Columbia.
41. MORRELL, S., VALERY, W., BANINI, G. and LATCHIREDDI, S. (2001). Developments in AG/SAG mill modelling. SAG 2001, Vancouver, pp 71-84, Dept of Mining and Mineral Process Engineering, Univ of British Columbia.
42. Alruiz, O. M., Morrell, S., Suarzo, C.J., and Naranjo, A., A novel approach to the geometallurgical modelling of the Collahuasi grinding circuit. Minerals Engineering (29 April 2009)
43. CLEARY, P., MORRISON, R. and MORRELL, S. (2001). DEM validation for a scale model SAG mill. SAG 2001, Vancouver, B.C., pp 191-206, Dept of Mining and Mineral Process Engineering, Univ of British Columbia.
44. CLEARY, P. W., MORRISON, R. D. and MORRELL, S. (2003). Comparison of DEM and experiment for a scale model SAG mill. International Journal of Mineral Processing Vol 68 (1-4): 129-165.
45. CLEMINSON, N. P., SOUTHWOOD - JONES, D. and MORRELL, S. (1994). Increasing capacity of a grinding circuit within the aid of computer simulation. Proc Chemeca '94, Perth, pp 719-725,
46. Daniel, M. J. and Morrell, S., 2004, “HPGR model verification and scale-up”, Elsevier, Minerals Engineering 17 (2004) 1149-1161, May (2004)
47. DELBONI, H. and MORRELL, S. (1996). The modelling of autogenous and semiautogenous mills. SAG '96, Vancouver, pp 713-728,
48. DUFFY, M. S. and MORRELL, S. (1997). Charge motion in tower mills. SME Annual Meeting, Colorado, pp 227-232,
49. Dunne, R. ; Maxton, D. ; Morrell, S. ; Lane, G., 2004, HPGR – The Australian Experience, Plant Operator’s Forum 2004: Things That Actually Work!, Society for Mining, Metallurgy and Exploration
50. DUNNE, R., MORRELL, S. and LANE, G. (2000). Design of the biggest mill in the world. After 2000-the future of mining, Sydney, NSW, pp 179-185, AusIMM.
51. DUNNE, R., MORRELL, S., LANE, G., VALERY, W. and HART, S. (2001). Design of the 40 foot diameter SAG mill installed at the Cadia gold copper mine. SAG 2001, Vancouver, pp 43-58, Dept of Mining and Mineral Process Engineering, Univ of British Columbia.
52. GOTTLEIB, P., MORRELL, S. and WELLER, K. R. (1994). Modelling grinding and liberation in tower mill regrind circuits used in lead/zinc concentrators. 8th European Symposium on Comminution, Stockholm, pp 761-772,
53. JANKOVIC, A. and MORRELL, S. (1997). Power modelling of stirred mills. Proc Inter Symp on Processing of Complex Ores , Mineral Processing and the Environment, Sudbury, Ontario, pp 195-208,
54. JANKOVIC, A. and MORRELL, S. (2000). Scale-up of tower mill performance using modeling and simulation. Proceedings of the XXI International Processing Congress, Rome,Italy, pp 1-7, Elsevier Science B. V.
55. KANCHIBOTLA, S. S., MORRELL, S., VALERY, W. and O'LOUGHLIN, P. (1998). Exploring the effect of blast design on sag mill throughput at KCGM. Mine to Mill 1998 Conference, Brisbane, pp
56. KANCHIBOTLA, S. S., VALERY, W. and MORRELL, S. (1999). Modelling fines in blast fragmentation and its impact on crushing and grinding. Explo '99, Kalgoorlie, WA, pp 137-144.
57. KARAGEORGOS, J., BURFORD, B., VALERY, W., ROHNER, P., JOHNSON, G. and MORRELL, S. (1996). Copper concentrator autogenous grinding practices at Mount Isa Mines Ltd. Proc SAG '96, Vancouver, pp 145-163,
58. KOJOVIC, T., MORRELL, S. and McKEE, D. J. (1997). Interdependancy of mine and mill. Proc of Crushing and Grinding Conf, Perth, pp 10,
59. KOJOVIC, T. and MORRELL, S. (1997). Surveying comminution circuits and ore characterisation. Proc of Crushing and Grinding Conf, Perth, pp 24,
60. KOJOVIC, T. and MORRELL, S. (1998). Prediction of product crusher shape.(Poster Paper). Comminution '98 conf., Brisbane, pp
61. LATCHIREDDI, S. R. and MORRELL, S. (1997). A laboratory study of the performance characteristics of mill pulp lifters. Minerals Engineering Vol 10 (11): 1233-1244.
62. LATCHIREDDI, S. and MORRELL, S. (1997). A new design of pulp lifter for grate discharge mills. Proc Sixth Mill Operators Conf, Madang PNG, pp 57-61,
63. LATCHIREDDI, S. R. and MORRELL, S. (2000). Influence of discharge pulp lifter design on slurry flow in mills. Mining Millennium 2000, Toronto, Canada, pp
64. LATCHIREDDI, S. and MORRELL, S. (2003). Slurry flow in mills: grate-only discharge mechanism (Part1). Minerals Engineering Vol 16 (7): 625-633.
65. LATCHIREDDI, S. and MORRELL, S. (2003). Slurry flow in mills: grate-pulp lifter discharge systems (Part 2). Minerals Engineering Vol 16 (7): 635-642.
66. LIM, W., MORRELL, S., TONDO, L. A. and DAVID, D. (1996). Modelling the high pressure grinding rolls. Proc of Mining Tech Conf, Fremantle, pp 169-176,
67. LYNCH, A. J. and MORRELL, S. (1992). The understanding of comminution and classification and its application in plant design and operation. Comminution - Theory and Practice. S. K. Kawatra pp 405-426.
68. McKEE, D. J., CHITOMBO, G. and MORRELL, S. (1995). The relationship between fragmentation in mining and comminution circuit throughput. Minerals Engineering Vol 8 (1265-1274).
69. MORRISON, R., KOJOVIC, T. and MORRELL, S. (1989). Modelling of SAG auto mill circuits. SAG Milling Seminar, Murdoch University WA, pp
70. MORRISON, R. and MORRELL, S. (1997). Evolution of AG/SAG milling technology. SME Annual Meeting, Colorado, pp 139-146,
71. MORRISON, R. and MORRELL, S. (1998). Comparison of comminution circuit energy efficiency using simulation. Minerals and Metallurgical Processing Vol 15 (4): 22-25.
72. NELSON, M., VALERY, W. and MORRELL, S. (1996). Performance characteristics and optimisation of the Fimiston (KCGM) SAG mill circuit. Proc SAG '96, Vancouver, pp 233-248,
73. NICOLI, D., MORRELL, S., CHAPMAN, B. and LATCHIREDDI, S. (2001). The development and installation of the twin chamber pulp lifters at Alcoa. SAG 2001, Vancouver, pp 240-255, Dept of Mining and Mineral Process Engineering Univ of British Columbia`.
74. OBENG, D. P. and MORRELL, S. (2003). The JK three product cyclone - performance and potential applications. International Journal of Mineral Processing Vol 69 (1-4): 129-142.
75. PARKER, B., ROWE, P., LANE, G. and MORRELL, S. (2001). The decision to opt for high pressure grinding rolls for the Boddington expansion. SAG 2001, Vancouver, B.C. Canada, pp 93-106,
76. POWELL, M. S., MORRELL, S. and LATCHIREDDI, S. (2001). Developments in the understanding of South African style SAG mills. Minerals Engineering Vol 14 (10): 1143-1153.
77. RADZISZEWSKY, P. and MORRELL, S. (1998). Fundamental discrete element charge motion model validation. Minerals Engineering Vol 11 (12): 1161-1178.
78. SCOTT, A., KANCHIBOTLA, S. S. and MORRELL, S. (1999). Blasting for mine to mill optimisation. Explo '99, Kalgoorlie, WA, pp
79. Scott, A., Morrell, S. and Clark, D., 2002, Tracking and quantifying value from “Mine to Mill’ improvement in Proceedings Value Tracking Sysmposium, AusIMM, Brisbane Australia, pp 77-84.
80. TONDO, L. A., MORRELL, S. and JOHNSON, G. (1995). A study of the energy consumption for grinding an Australian gold ore in a high pressure roll machine. Proc XVI Encontro Nacional de Tratmento De MInerios E Hidrometalurgia, Rio, Brazil, pp 65-79,
81. VALERY, W. and MORRELL, S. (1995). The development of a dynamic model for autogenous and semi autogenous grinding. Minerals Engineering Vol 8 (11): 1285-1297.
82. VALERY, W., KOJOVIC, T., TAPIA-VERGARA, F. and MORRELL, S. (1999). Optimisation of blasting and sag mill feed size by application of on line size analysis. IIR Crushing and Grinding Conference, Perth (29-31 March), pp
83. VALERY, W., MORRELL, S., KOJOVIC, T., KANCHIBOTLA, S. S. and THORNTON, D. M. (2001). Modelling and simulation techniques applied for optimisation of mine to mill operations and case studies. VI Southern Hemisphere Meeting on Mineral Technology, Rio de Janeiro, Brazil, pp 107-116, CETEM/MCT.
84. WELLER, K. R., MORRELL, S. and GOTTLEIB, P. (1996). Use of grinding and liberation models to simulate tower mill circuit performance in lead/zinc concentrator to increase flotation recovery. Inernational Journal of Mineral Procesing Vol 44-45: 683-702.
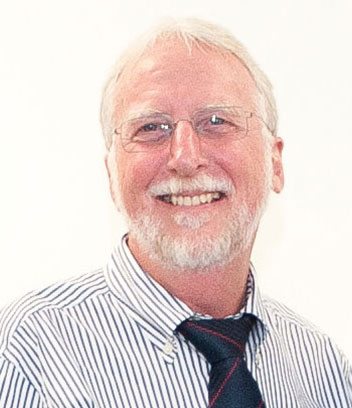